Společnost Yaskawa nabízí portfolio produktů, díky kterým je předním výrobcem v oblasti měničů střídavého proudu, servopohonů, řídicí technologie a robotiky.
Vysoce flexibilní robotická svařovací buňka pro maximální výkon
- Průmyslové odvětví
- Automobilový průmysl
- Aplikace
- Obloukové svařování
- Kient/ zákazník
- AL-KO
- produkty
- RWV2 - Polohovadla
- AR1440 - AR řada
Robotické duo zvládlo 1 000 variant
Nápravy a rámy pro užitkové přívěsy, obytné vozy a mobilní domy od společnosti AL-KO Vehicle Technology patří k tomu nejlepšímu, co je na trhu k dispozici. Výrobci po celém světě těmto komponentům důvěřují. Tomu odpovídají i vysoké nároky na svařovací techniku, včetně prvotřídní kvality švů a vysoce flexibilní systémové techniky s roboty, které pracují přesně a procesně spolehlivě.
Skupina AL-KO Vehicle Technology Group je globální technologickou skupinou. S vysoce kvalitními komponenty karoserií a podvozků pro přívěsy, rekreační a užitková vozidla i stavební a zemědělská vozidla je skupina vizitkou nejlepší funkčnosti, nejvyššího komfortu a inovací pro vyšší bezpečnost při manipulaci. Skupina zaměstnává více než 3 800 pracovníků na 30 místech po celém světě a vykazuje roční obrat blížící se miliardě amerických dolarů.
Navzdory globalizaci a expanzi této úspěšné společnosti se osvědčené komponenty přívěsů AL-KO - od nájezdových zařízení až po kompletní nápravy - tradičně vyrábějí v jejím hlavním sídle ve švábském městě Kötz.
Zejména svary při výrobě rámů jsou vystaveny vysokému dynamickému zatížení a spojování těchto komponentů patří k nejnáročnějším úkolům ve spojovací technice. Spolehlivý svařovací proces a nejmodernější systémové inženýrství jsou zde nepostradatelné, aby byla zaručena maximální kvalita komponentů při zachování neomezené flexibility.
Pro výrobu příčníků pro užitkové přívěsy s celkovou hmotností až 3,5 tuny používá společnost AL-KO novou, průkopnickou svařovací buňku, ve které paralelně svařují dva roboty Motoman. Celkový vývoj svařovací buňky je společným projektem společností AL-KO a Yaskawa. Výchozím bodem byla standardizovaná specifikace švábského výrobce, která předdefinovala klíčové parametry, včetně energetické účinnosti, bezpečnostní techniky, procesních časů a kvalitativních standardů.
Maximum flexibility with minimum space requirements
Planning the installation became a real challenge due to two restrictions, as Steffen Schumacher, production and investment planner at AL-KO, reflects: “Firstly, very limited space was available for the complete installation, so that we had to be extremely inventive in order to realize the project at all. Secondly, the systems engineering had to guarantee a maximum of flexibility, as about 1,000 variants were to be welded by robot.”
Because only cross members for the aforementioned utility trailers were to be manufactured on the system, the extremely high number of variants may at first sound almost unbelievable. But if we consider that AL-KO serves over 50 small and large customers, this size is somewhat relativized. The spectrum is only limited by sheet metal thicknesses, which are between two and three millimetres.
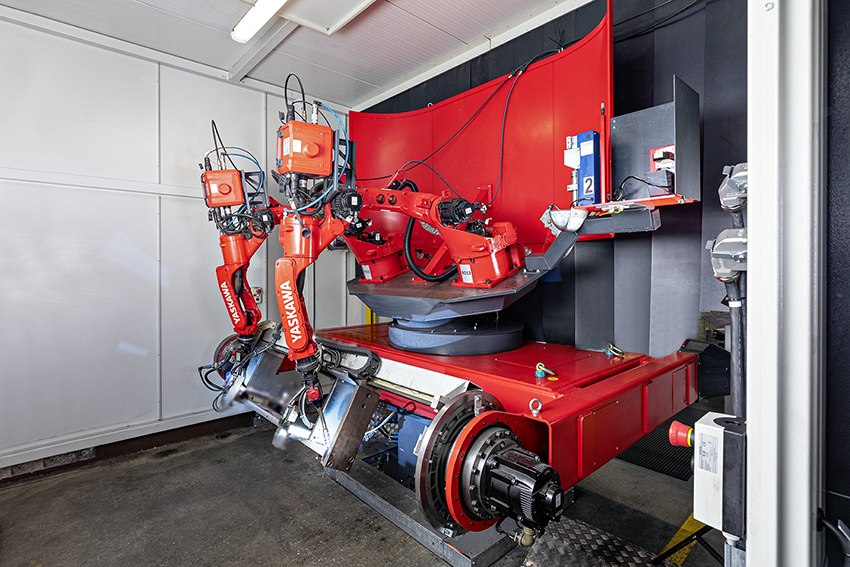
The concept of ultra-short delivery times
The company's claim to being able to deliver to customers within five days of placing their order calls not only for unbelievable flexibility, but also for the provision of corresponding manufacturing capacities together with extensive and expensive warehousing. Schumacher comments: “This customer service of short delivery times is, of course, a real challenge. However, customer orientation is also a unique selling point, appreciated by trailer manufacturers all over the world. Our task is to create structures with innovative production and intralogistics concepts that make this strategy of short delivery times possible.”
With the new welding unit, in which two slim Motoman Type MA1440 six-axis robots are in operation, AL-KO has shown how such solutions look in practice. Each robot has its own burner cleaner and wire cutter. The robot controller is a Yaskawa DX200. A three-axis H-table from Yaskawa’s standard programme serves as a positioner. The control of the complete installation is assumed by a user-friendly Siemens SPS S7, on which many welding programmes for the variants are now stored. The user only has to select a suitable programme and start the process.
The planners proposed an unusual solution to effectively compensate for the limited space. Yaskawa Sales Manager Roland Hermann remembers: “When we realised the extent of the spatial restrictions, it was clear in these circumstances that all registers would have to be pulled in order to find an easily accessible solution. Finally, the idea of mounting the two robots on the H-table led to success. The elevated working position of the robots also ensures perfect access to the welded assemblies. The complete cell is just 4.2 metres wide and 4.7 metres long.”
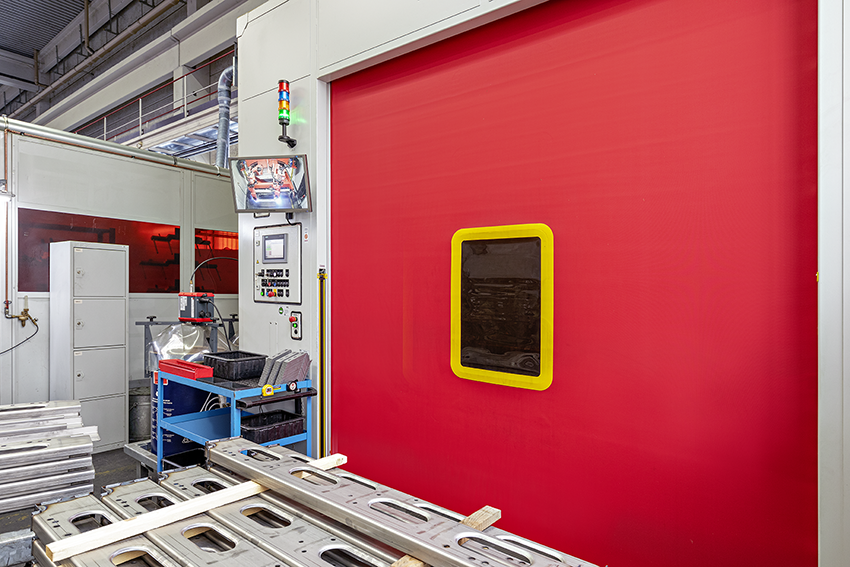
Top quality welding seams
Because AL-KO places a strong emphasis on weld seam quality, requiring that the welds meet the highest technical and visual standards, only premium welding technology was acceptable. “Specifically, we weld the holding brackets on the traverses, through which these cross-members are bolted to the longitudinal members of the trailer. This connection is safety-relevant, which is why a process-reliable, first-class welding result is vital here,” says Schumacher.
Not least because of this, the decision was made in favour of renowned manufacturer Fronius, which contributed both the welding power source TPS 500i and the water-cooled robot burner. The CMT technology employed here guarantees a largely spatter-free welding process with low component distortion.
Furthermore, the use of two robots radically reduces component distortion, although this solution was realised mainly due to the substantially shorter welding times.
Simple operation of the unit
There are no big surprises concerning operation of the unit: While the robots are welding on one side of the unit, an employee is busy with the removal of the finished parts and insertion of new components on the other side of the H-table. Cycle times vary considerably depending on the variant, but the removal and insertion work is always guaranteed to take less time than for the welding process itself. The Motoman welding robots can demonstrate their impressive dynamism to the full without waiting times. Downtimes are determined only by the rotation of the H-table.
As far as the batch sizes on the unit are concerned, the many variants are not exactly a positive factor. “Nevertheless, we managed to achieve an average batch size of 27. Roughly speaking, batch sizes lie between 10 and 100 components. Even smaller quantities are not really profitable to produce by automated means and, if unavoidable, these are manufactured by manual welding,” stresses Gökhan Kocak, AL-KO production manager in frame part manufacturing.
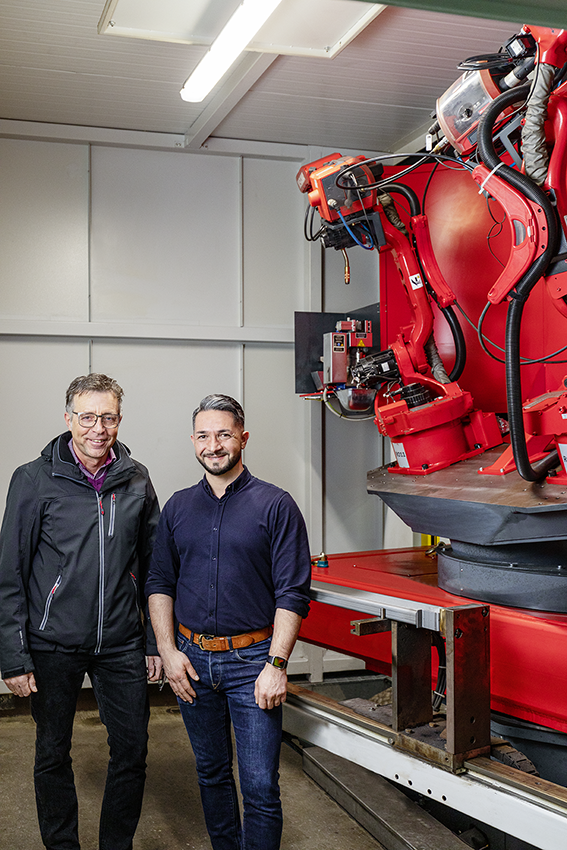
All targets met
The welding results reliably delivered by the unit do not fail to satisfy the high expectations. This is proven by first- and final part sampling, obligatory for every production order in frame part manufacturing. In addition, the system operator – responsible for manually loading and removal the parts – performs a visual inspection of each component.
Schumacher sums up: “As no other robot manufacturer, Yaskawa stands for welding quality and process reliability. The two welding robots demonstrate an impressively high level of dynamism and precision. Thanks to their slim design, they cope very well with the lack of space. All in all, with the jointly developed unit we were able to optimally meet our targets.”
Text: Ralf Högel
Contact readers’ enquiries
Tel. +49-8166-90-0
Fax +49-8166-90-103