Společnost Yaskawa nabízí portfolio produktů, díky kterým je předním výrobcem v oblasti měničů střídavého proudu, servopohonů, řídicí technologie a robotiky.
Reduced Labor Costs and Added Production Shift by Festo Polymer
Flexible workpiece feeding enables maximum utilization of an existing production facility
Manual insertion of unsorted and unpositioned parts is still common in German manufacturing processes. Those manual procedures are very labor-intensive and expensive, especially when operating multiple shifts. The automation potential in this area is, thus, enormous. Key factors for the decision to automate are high productivity and reliability, and a quick return on investment with maximum flexibility for changing tasks. This is where the standard automation system SUMO Fotoplex of EGS Automation, a brand of AMETEK, comes into play.
- Průmyslové odvětví
- Chemie/ Plasty
- Aplikace
- Pick & Place
- Kient/ zákazník
- EGS Automation GmbH
- produkty
- GP7 - GP řada
Festo Polymer, a subsidiary of the Festo Group, employs over 20,000 people across more than 250 locations worldwide. The St. Ingbert site in Saarland includes multiple units, one of which is the Global Production Center (GPC) in Hassel. This modern, 15,000-square-meter facility employs over 200 people and specializes in producing highly automated plastic parts for the parent company using more than 60 injection molding machines. Some parts are also assembled into modules. These components are integrated into the world-renowned pneumatic products bearing the iconic blue company logo. Given the extensive product range and the need for long-term spare parts supply, the number of product versions, storage capacity, and maintenance requirements for injection molding tools are immense.
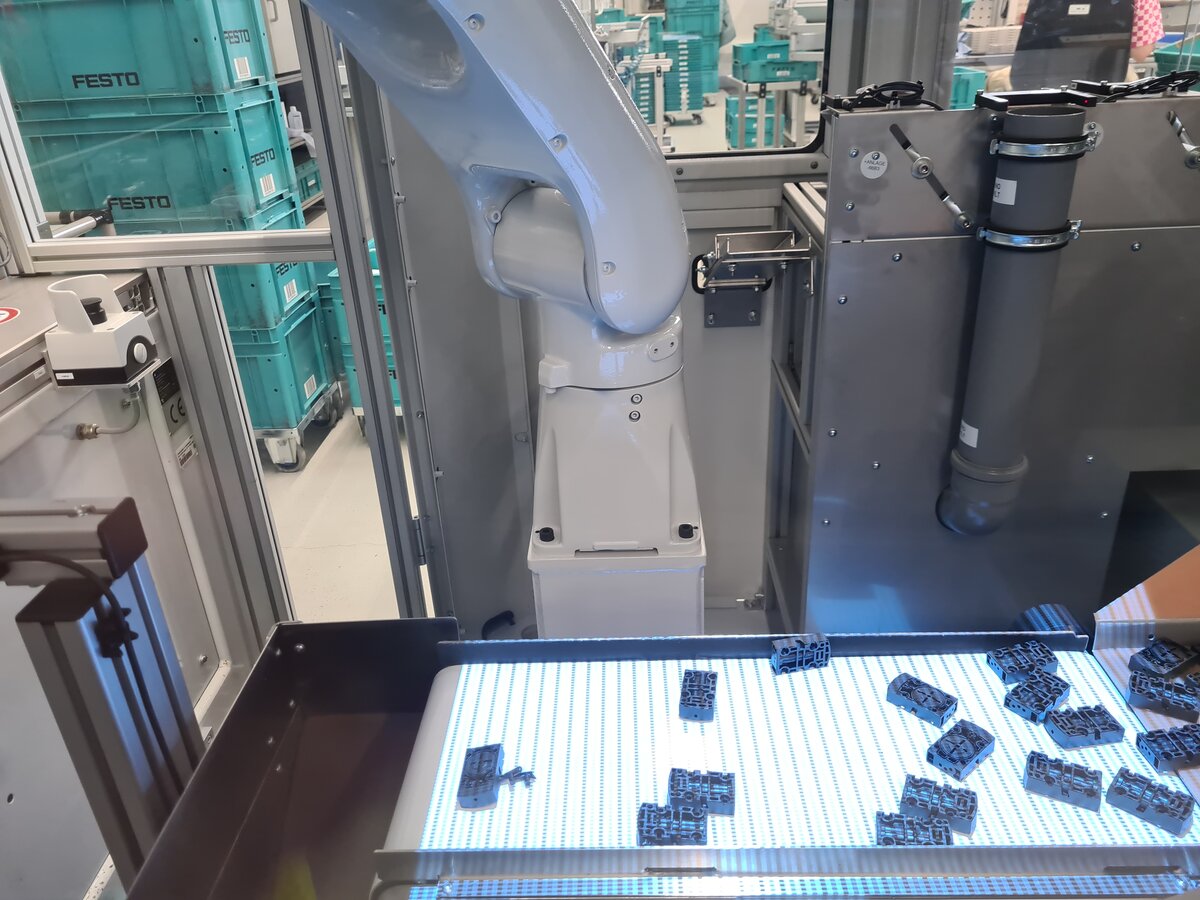
Picture: Position detection of the magnetic lids
“We produce over 3,500 different product variants here, some of which have remained unchanged in design for decades. This diversity underscores the critical role of our Industrial Engineering team.” Peters proudly highlights the various awards his team has received. Alongside production process planner Steffen Hess, who optimizes and automates value streams, and production engineer Sascha Kunz, responsible for project planning and calculation, Peters showcases the various departments at Hassel. These include injection molding production, rubber production, surface treatment/painting, industrial engineering and tool service, office and administration, and central material supply logistics. And finally, the assembly area, where an EGS Automation SUMO photoplex cell was installed at the beginning of 2024 to equip a balling process.
Since 1996, EGS Automation, based in Donaueschingen, has developed custom automation solutions and standardized automation cells under the SUMO product family. Most of the more than 2,300 installed robot solutions operate in the metal and plastics industries, offering customers the advantage of extensive experience. This expertise led Festo Polymer to choose EGS Automation for a reliable, standardized, and flexible feeding system.
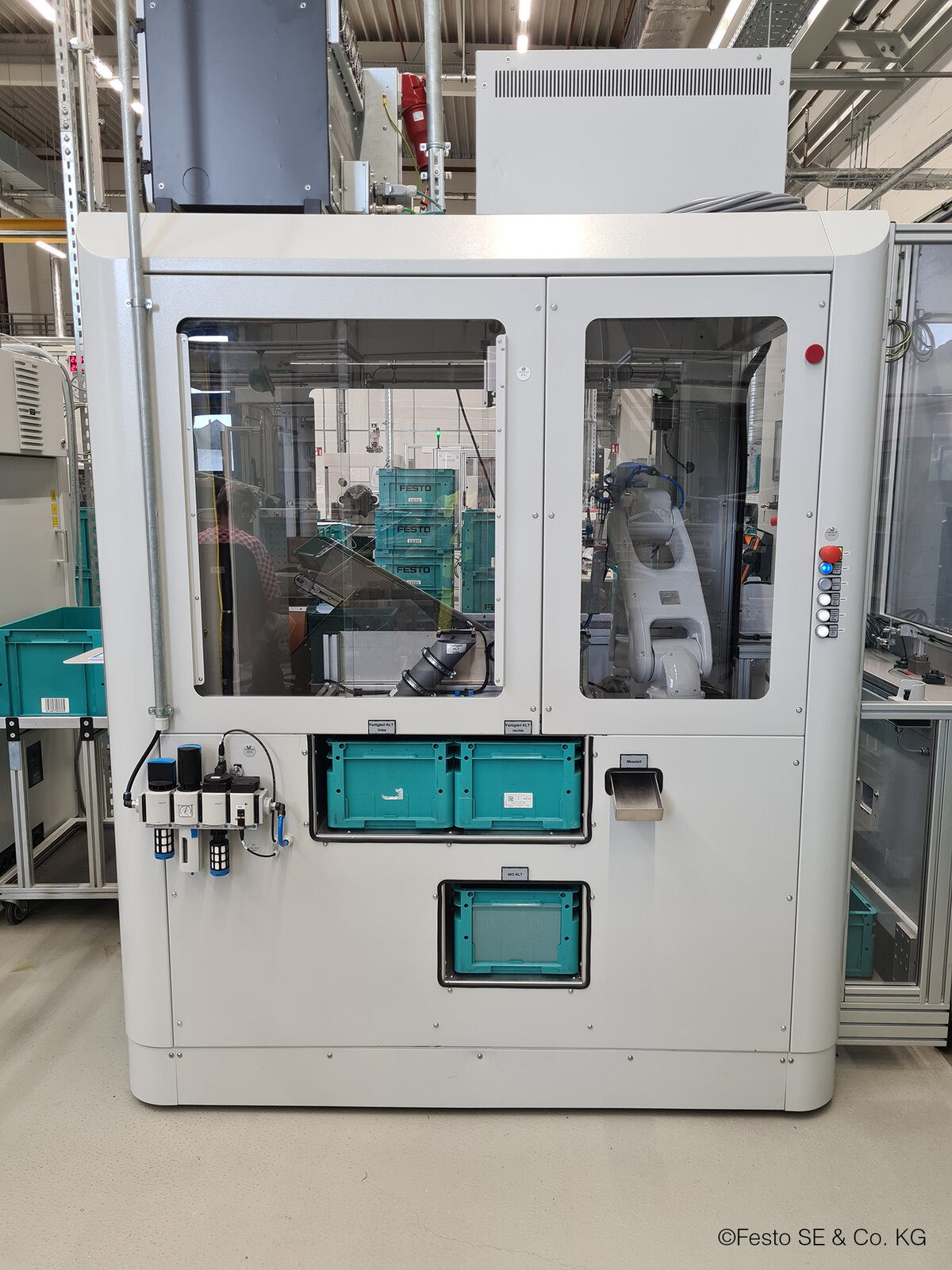
Picture: The SUMO Fotoplex fully integrated in the SUMO all-in-one system housing
"EGS Automation outperformed four other potential suppliers in our value analysis," notes Sascha Kunz. "We were impressed by their sophisticated concept, excellent presentation, and a visit to another EGS customer’s implementation. Additionally, the delivery time EGS could offer due to its standardized concept was a decisive factor for us."
The automation task involved feeding a plastic part into an existing automatic balling process in a position-oriented, precise, and reliable manner. Small metal balls are pressed into several holes in a magnetic lid component. The magnetic lids, produced by an injection molding machine in the same factory, are fed into the system unsorted as bulk material. This task is ideal for the SUMO Fotoplex from EGS, a flexible feeder that uses industrial image processing for component and position detection. The modular design within the modern all-in-one SUMO system housing allows for different feeder configurations, from classic feeder concepts to rotary systems and pure bin picking versions.
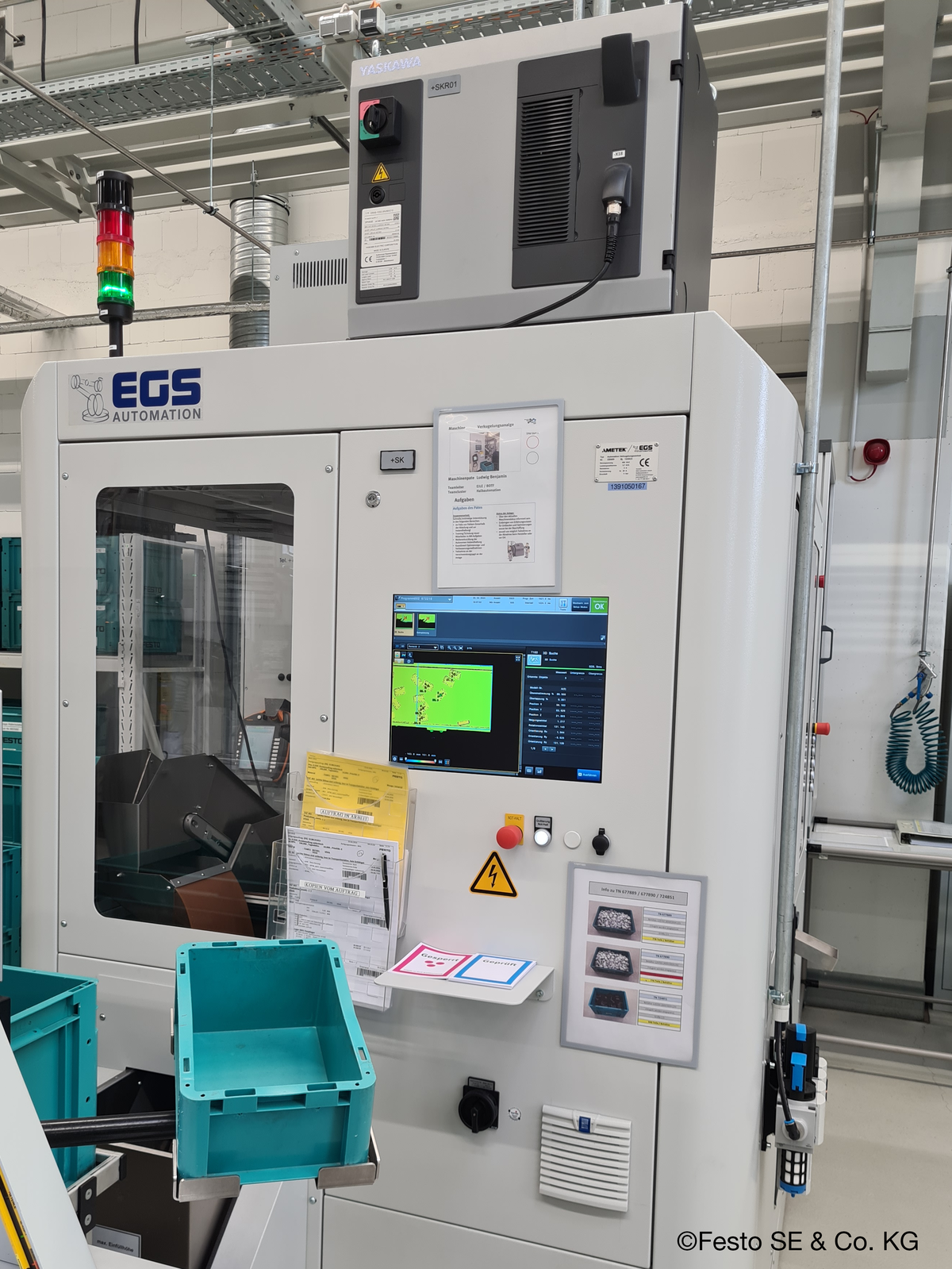
Picture: The integrated monitor on the SUMO Flexiplex shows the current position of the parts in the feeder at all times
Components, roughly the size of a matchbox, are loaded into a component hopper. From there, they are transferred to a conveyor belt system via an ascending conveyor, ending on a belt in the detection area of the 3D image processing system. Thanks to the belt's backlighting and the optical encapsulation of the entire cell, the process is completely insensitive to ambient light. Foreign parts, such as sprues that accidentally enter the parts supply, are sorted out, ensuring the system's reliability.
The position of the components is relayed to a Yaskawa MOTOMAN GP7, a six-axis robot that picks up the components from the belt, rotates them if necessary, and places them in the desired position in a separate machine. The Festo site in Hassel already uses several Yaskawa robots, which are renowned for their reliable operation, low maintenance costs, and ease of use. After depositing the parts, the robot moves to the balling system's insertion position, removes a finished part, and inserts the new one. The system features a two-station shuttle table, allowing loading and unloading without affecting cycle times. The two-hand control panel from before the process was automated remains in the system as an emergency strategy in case of potential failure.
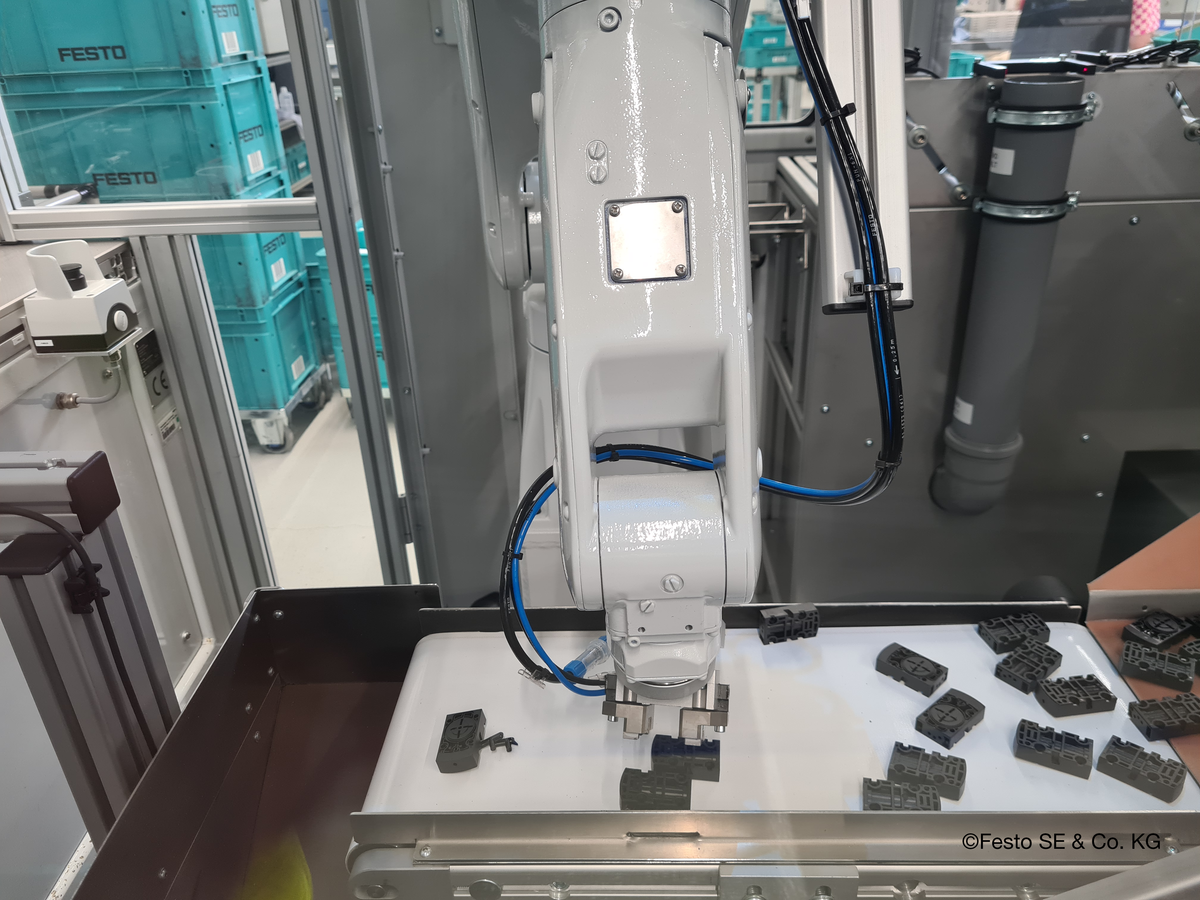
Picture: The robot receives the exact position of the magnetic lids and picks them up from the conveyor belt
"The component is a high-demand item, critical for our delivery capability," says Steffen Hess. "Therefore, having an emergency plan was essential. EGS provided excellent support in coordinating the interface with the balling system manufacturer, making it easy to retain the option for manual operation in emergencies." Finished components are discharged into containers via chutes, while rejected parts are sorted into a separate container. A dedicated measuring output is also available for double-checking finished parts if needed.
Currently, three product versions are implemented in the feeding solution at Festo Polymer, with another version to be added soon in-house. “Through detailed training by EGS Automation, we have gained all the necessary knowledge. Should we need additional support, EGS is available to provide further advice. This allows us to utilize our own expertise while relying on experienced support when needed," says Hess.
The spherical valve cover is used in Festo's valve terminals which again is a key component in the solution implemented by EGS Automation, effectively closing the loop on their use.
A data interface provides the necessary information for integration into the in-house MES system, allowing for monitoring and evaluation of the solution's proper operation.
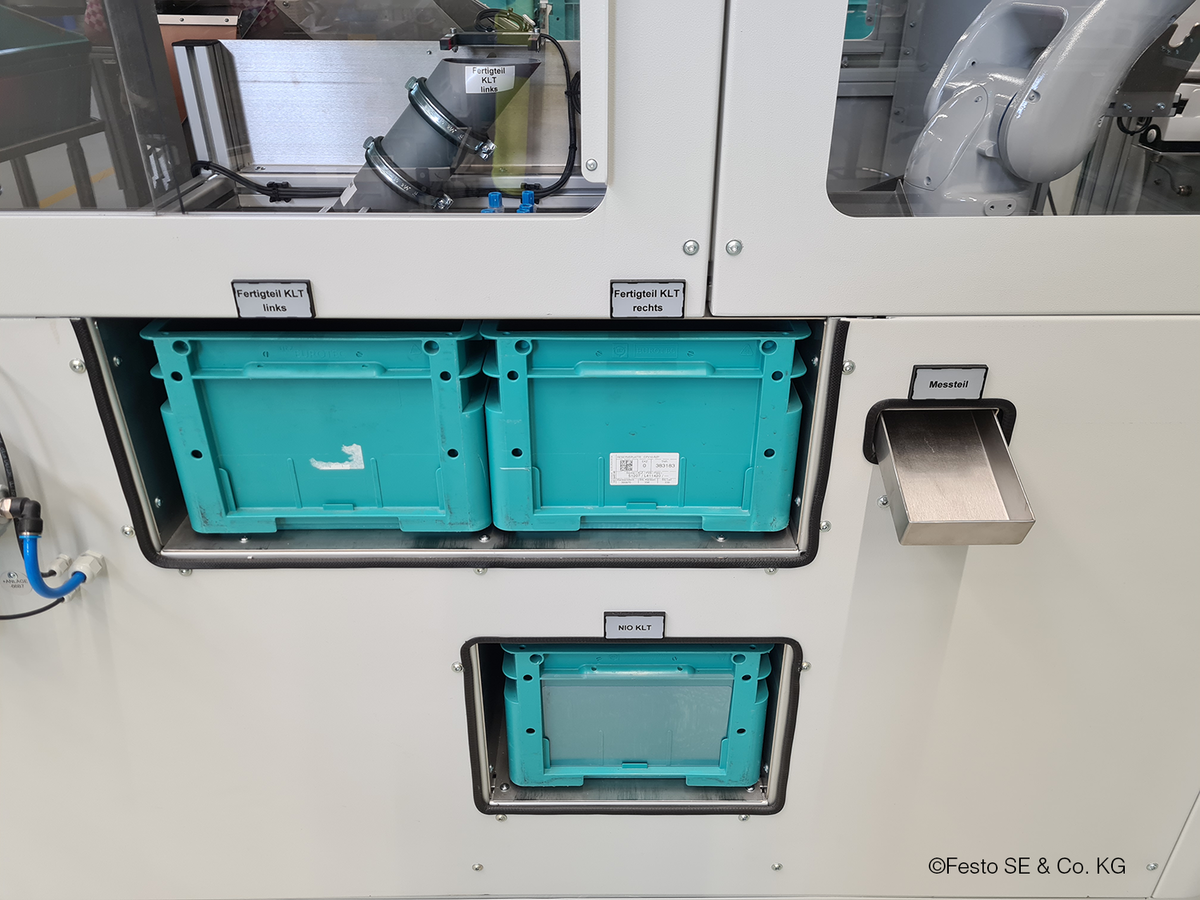
Picture: Finished parts and niO parts are dispensed in containers that can be easily removed. Measured parts are dispensed on request
The results are overwhelmingly positive. The number of staff required to operate the balling system at Festo Polymer has been drastically reduced. The system runs so consistently and with so few errors that it can be refilled before the weekend and continue for some time. Previously, the system required manual operation with employees working in two shifts. With automation, an additional production shift has been added while personnel costs have decreased. Employees who previously loaded the system manually are now engaged in more demanding tasks, utilizing their time more effectively. "The acceptance of the new system as a tool for performing monotonous tasks is very high," says Christian Peters. This positive sentiment is evident in the group photo taken in front of the system, showing everyone involved in high spirits.
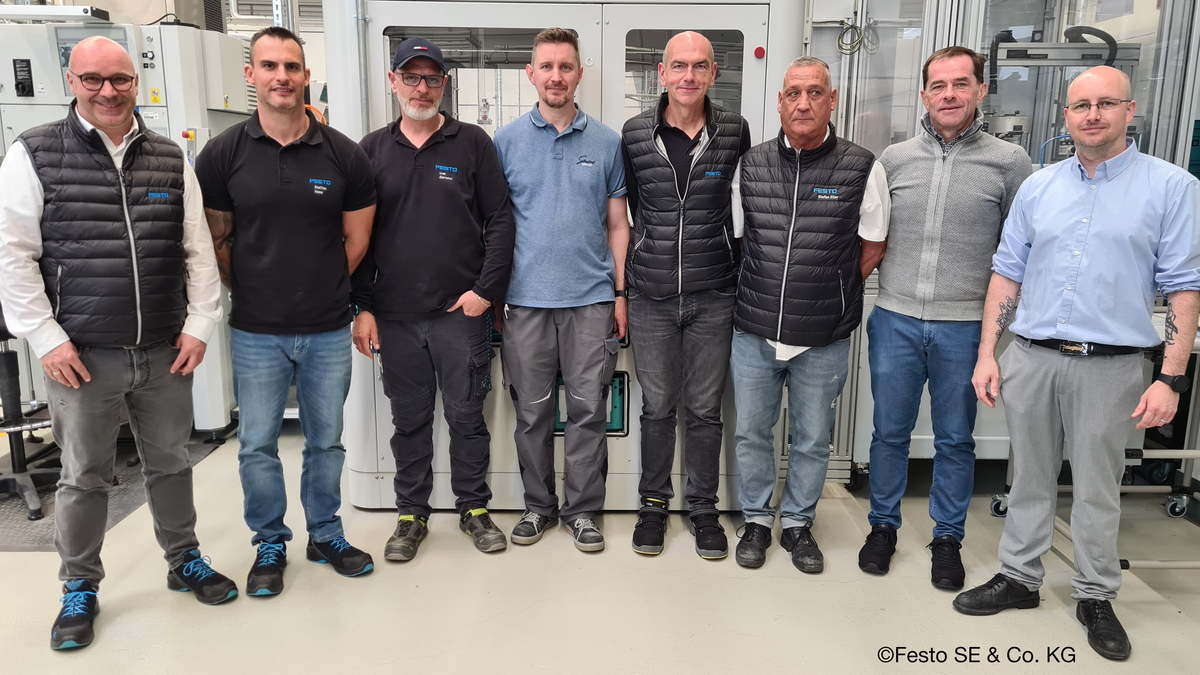
Picture: Everyone involved in the project is completely satisfied and the acceptance of the system, which relieves them of monotonous tasks, is very high.
EGS Automation GmbH
Raiffeisenstr. 2
78166 Donaueschingen
Germany
Phone +49 771 898606-0 | Telefax: +49 771 898606-99
egs.info@ametek.com | https://www.egsautomation.de/
Your contact for Public Relations:
Stefanie Tröndle
Stefanie.Troendle@ametek.com
Pictures and Text: ©Festo SE & Co. KG, all rights reserved