Společnost Yaskawa nabízí portfolio produktů, díky kterým je předním výrobcem v oblasti měničů střídavého proudu, servopohonů, řídicí technologie a robotiky.
Inovativní robotická svařovací buňka zajišťuje maximální flexibilitu
- Průmyslové odvětví
- Obrábění kovů
- Aplikace
- Obloukové svařování
- Kient/ zákazník
- Arburg
- produkty
- AR2010 - AR řada
Řešení pro velikost šarže 1
Renomovaný výrobce vstřikovacích strojů Arburg poskytuje důkaz, že velikost šarže 1 a plná automatizace se vzájemně nevylučují, a to prostřednictvím průkopnického robotického svařovacího systému. Naopak: V centrále v Lossburgu se takové výzvy řeší efektivně a hospodárně.
Společnost Arburg byla založena jako malá firma v idylickém Schwarzwaldu v roce 1923, dosáhla velkolepého vzestupu a stala se jedním z předních světových výrobců strojů na zpracování plastů. Rodinný podnik má v současné době celosvětově přibližně 3 200 zaměstnanců a stále vyrábí výhradně v Lossburgu - nyní na ploše přes 170 000 m2 a s mimořádně vysokým vertikálním rozsahem výroby kolem 60 %.
Vysoce kvalitní univerzální vstřikovací stroje s hydraulickou, hybridní, elektrickou nebo vertikální technologií vstřikování jsou velmi žádané. Exportní kvóta ve výši přibližně 70 procent podtrhuje mezinárodní respekt, kterému se tyto stroje těší. Automatizační technologie používaná při jejich výrobě je stejně inovativní jako samotné univerzální vstřikovací stroje.
Robotická svařovací buňka ve své třídě
Ukázkovým příkladem nejmodernější výrobní technologie ve společnosti Arburg je výroba plechů. Právě zde se vyrábějí strojní stojany pro vstřikovací stroje, které váží tuny, a to ve všech možných provedeních. Wolfgang John, vedoucí oddělení nestříhané výroby, shrnuje speciální vlastnosti výrobní techniky: "Zde vyrábíme výhradně na zakázku zákazníka, což často znamená velikost dávky 1 vzhledem k širokému sortimentu a modularitě našich vstřikovacích strojů. K tomu potřebujeme robotickou svařovací buňku s maximální flexibilitou, kde je nezbytné offline programování, maximální dostupnost a spolehlivost procesu, stejně jako prvotřídní výsledky svařování."
Specialisté na svařování ze společnosti Yaskawa Europe se zde postarali o běh. A to, co v úzké spolupráci s manažery společnosti Arburg v Lossburgu nainstalovali, je působivé: Na velmi omezeném prostoru se nachází špičková svařovací buňka, dlouhá přibližně 11 metrů a široká 4,5 metru. Na jejím portálu X-Y-Z je zavěšen šestiosý robot Motoman MA2010. Dva speciální rotační polohovadla vyzvedávají pomocí vhodných nosičů přípravků předem připravené, až 5 500 milimetrů dlouhé a tři tuny těžké strojní stojany, které pak svařovací robot svařuje v plynovém ochranném štítu MAG v dokonalé žlabové poloze.
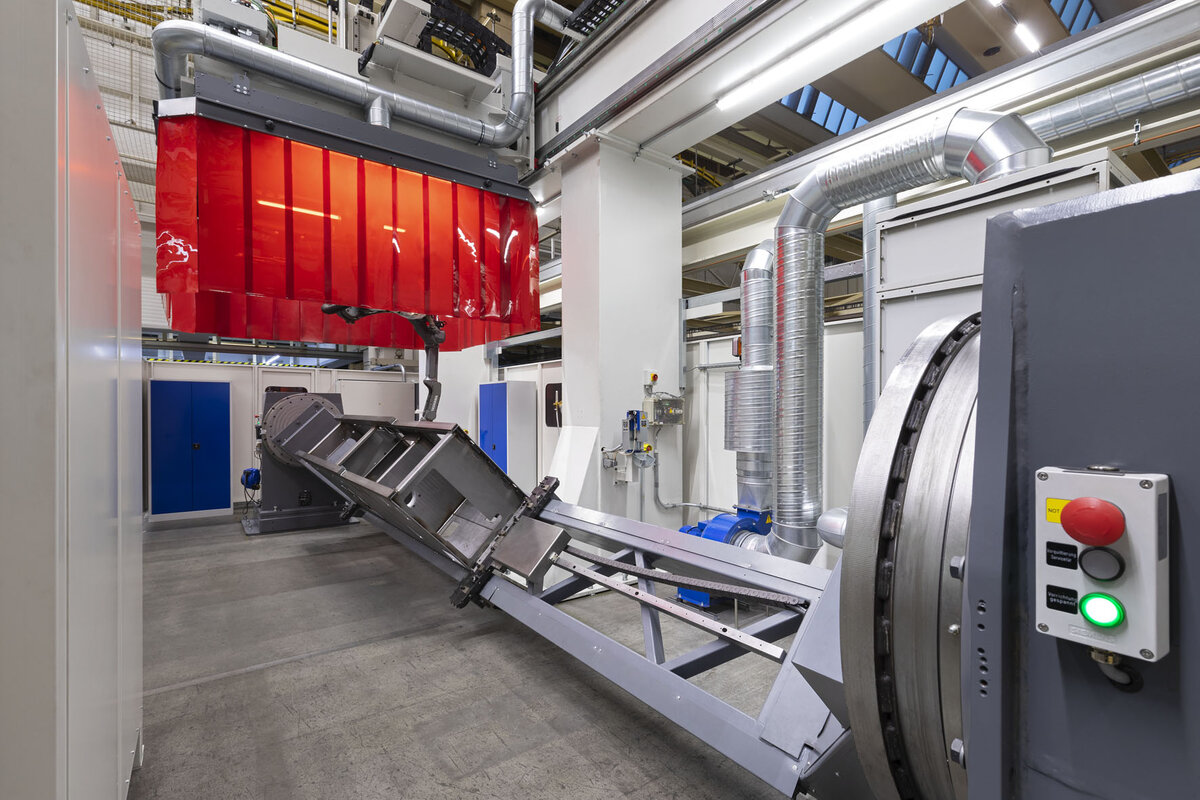
Up to 100 meters of weld seam per component
All machine stands are made of the sheet metal material S235, whereby the material thicknesses vary between five and eight millimetres depending on the model. A 500 ampere welding source by Lorch and a water-cooled welding torch in combination with the path-precise and dynamic Motoman robot guarantee high welding speeds and first-class seam quality: "We draw welds of up to 100 meters per component. Here we depend on efficiency and reproducible quality. The welding seams not only have to meet visual requirements, but also have to be permanently leak-proof, especially in the case of containers for hydraulic oil," says Wolfgang John.
In practice, one can only marvel at how dynamically the slim welding robot with its internal hose package does its work. Even in corners or tight radii, the MA2010 hardly needs to reduce its welding speed. Largely spatter-free welding shows how safely controlled the process is. The DX200 controller smoothly handles the synchronization of the total of eleven NC-controlled axes - six of the robot, three of the gantry and two of the positioner.
The lot size 1 challenge
However, the greatest challenge for the plant is the small batch sizes, which increasingly tend to be lot size 1. Nevertheless the company is well equipped to deal with unproductive set-up times, as Martin Braun, the Arburg Group Manager for Electrical Equipment Design, assures: "We consistently rely on the opportunities provided by offline programming. In addition, we have invested a great deal of creativity in the design of an intelligent fixture carrier with a highly flexible clamping system that allows us to securely clamp all machine stand variants simply within minutes. This is the only way we can meet the challenge of batch size 1."

Offline programming makes the impossible possible
Arburg uses Yaskawa's MotoSim offline programming system for programming new components on the computer and the operators are very enthusiastic about the system. It permits designing a realistic 3D simulation by using the same kinematic model as the DX200 robot controller. The programming language is also identical, making it possible to completely develop welding programs offline. "With MotoSim we reduce the programming times considerably and limit the effort for final on-system teaching by about 80 to 85 percent", says Martin Braun.
At present, almost 100 machine stand variants are stored in the memory of the control system, more will follow. After the changeover from one component to the next, the operator only has to select the appropriate program and the robot carries out its welding program. In order to ensure the highest level of safety, the welding cell is equipped with a wide range of sensors and special measuring equipment to ensure system geometry. This means that each individual robot axis can be measured individually by approaching special calibration points and, of course, sensors monitor the secure clamping of components weighing several tons. Industry 4.0 at its best.
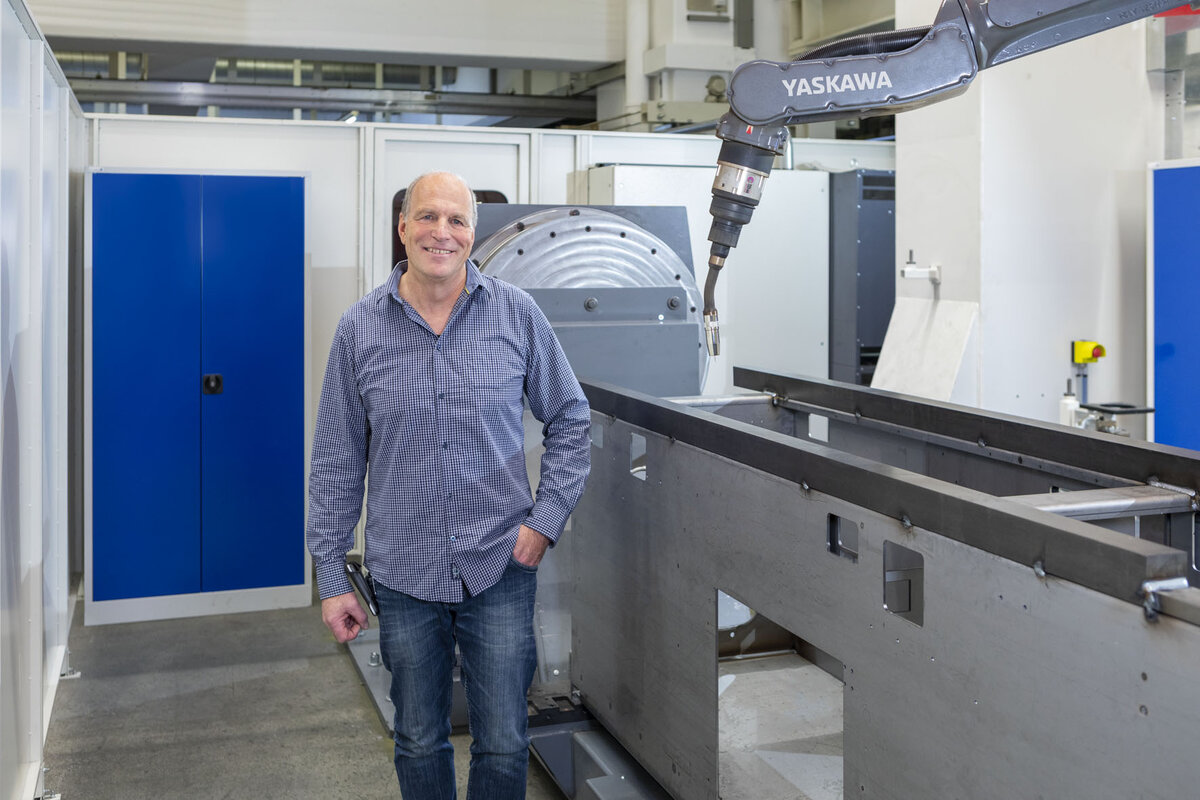
Cooperation and partnership as a factor for success
The know-how of the Arburg team, which has developed over decades, made a decisive contribution to the fast and uncomplicated commissioning of the plant. The specialists from the Black Forest with experience in robotics also get on very well with the welding cell during operation. And robots and components from the Japanese supplier are also renowned for their reliability. So it’s no surprise that the plant has been operating reliably since its commissioning in August 2019 and that it has met the high expectations.
Even though the demand for external services will remain manageable in the long term - Arburg has an excellent maintenance team - the Black Forest company is particularly keen to maintain a good relationship with its suppliers: "We have been using Yaskawa products for many years and value their quality. But we also know that we can rely on Yaskawa's support in an emergency. And that’s what counts," concludes Wolfgang John.
Text: Ralf Högel
Contact readers’ enquiries
Tel. +49-8166-90-0
Fax +49-8166-90-103